Hydrographic Printing Services
What Is Hydrographic Printing?
Hydrographic printing, also known as water transfer printing, is an innovative coating process that allows for the application of intricate designs and patterns onto a variety of surfaces. This technique involves transferring a printed film onto an object submerged in water, resulting in a seamless and highly detailed finish.
The primary advantages of hydrographic printing include its versatility, enabling customization on complex shapes and materials, as well as its ability to produce stunning visual effects that enhance the aesthetic appeal of products. Common applications range from automotive interiors and sporting equipment to consumer electronics and home decor.
Looking for a partner for your hydrographic printing needs?, PaintKing stands out as a leader in the industry. Our advanced technology, coupled with a skilled workforce, ensures exceptional quality and precision in every project. Trust PaintKing to deliver innovative hydrographic printing solutions that elevate your products and captivate your audience.
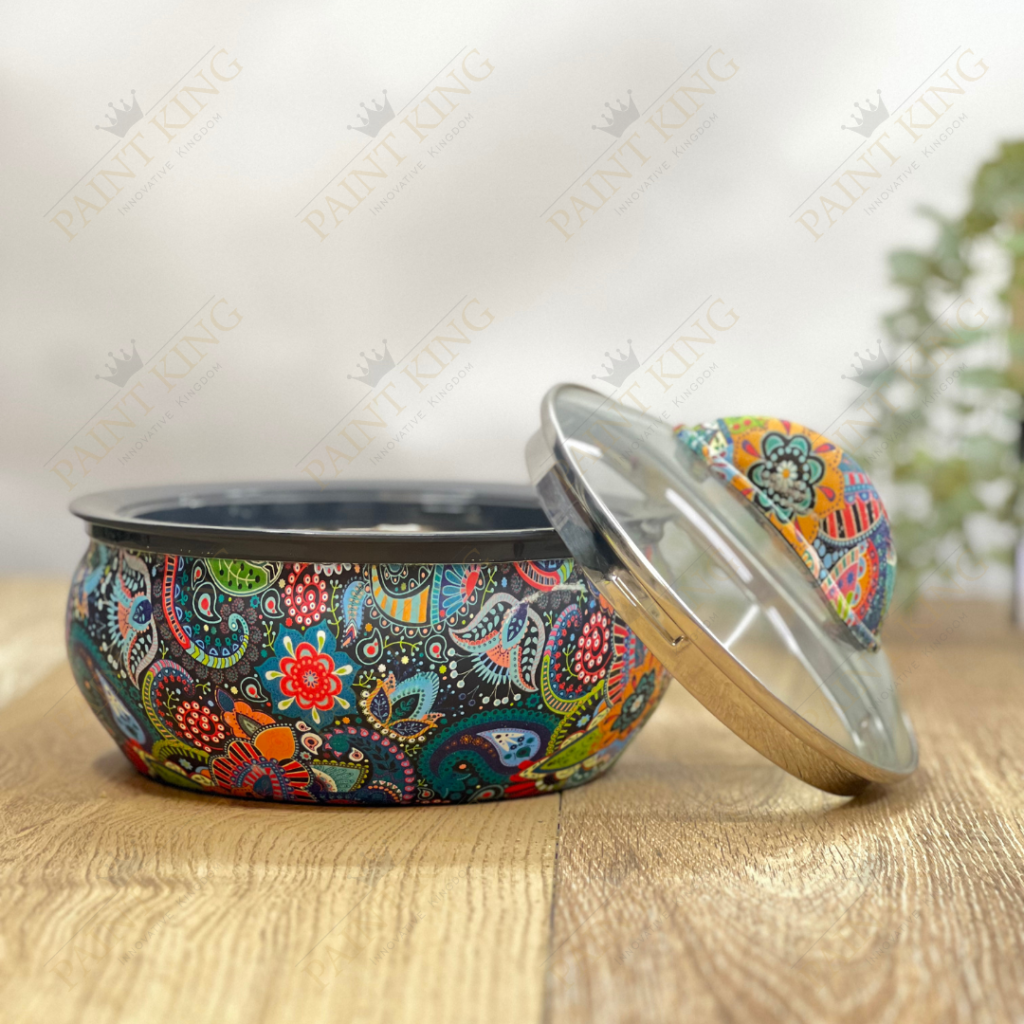
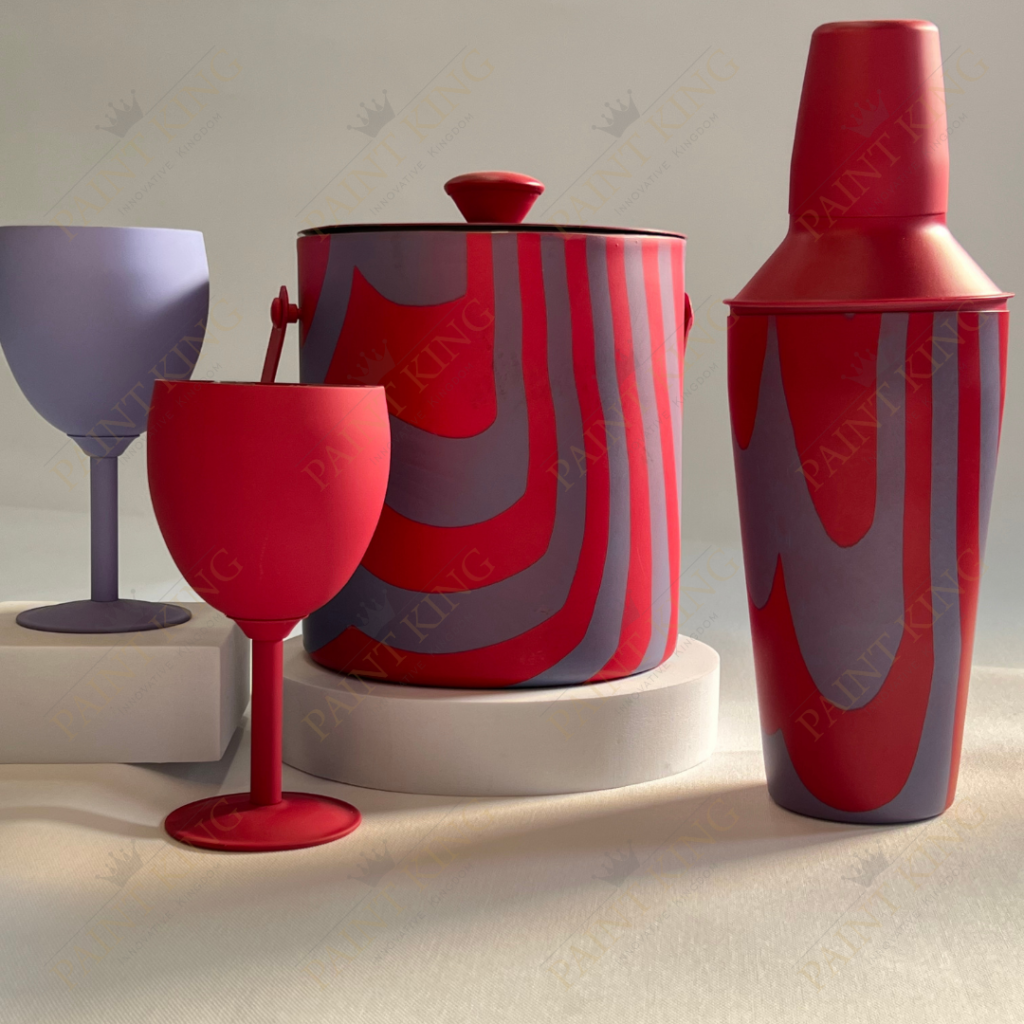
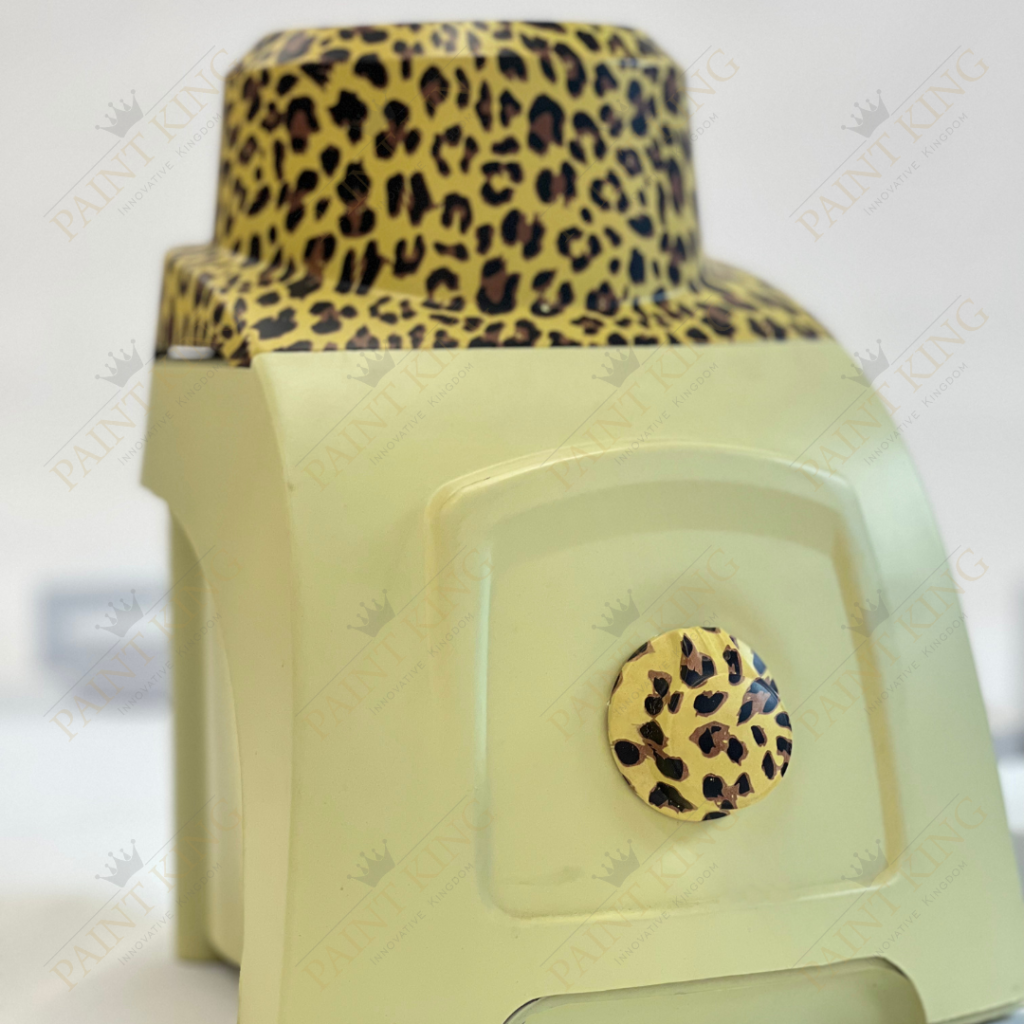
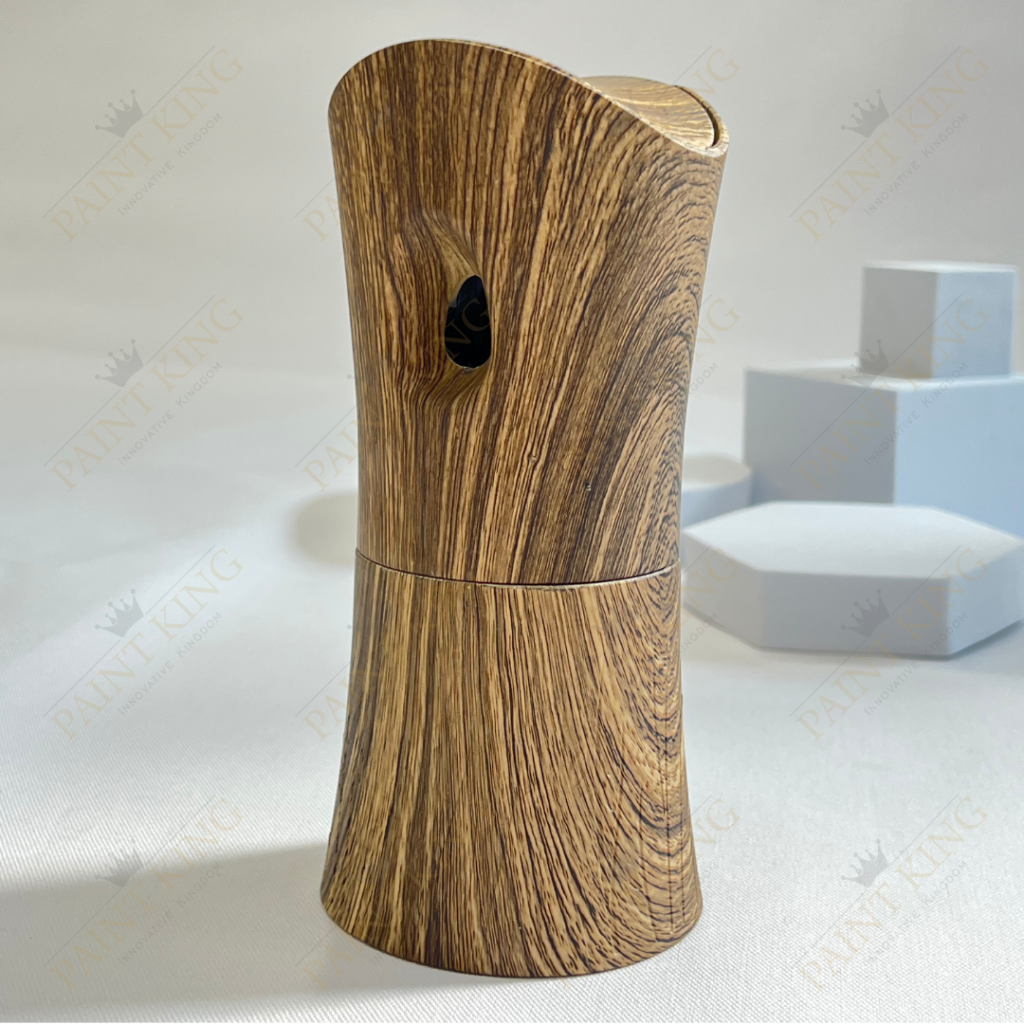
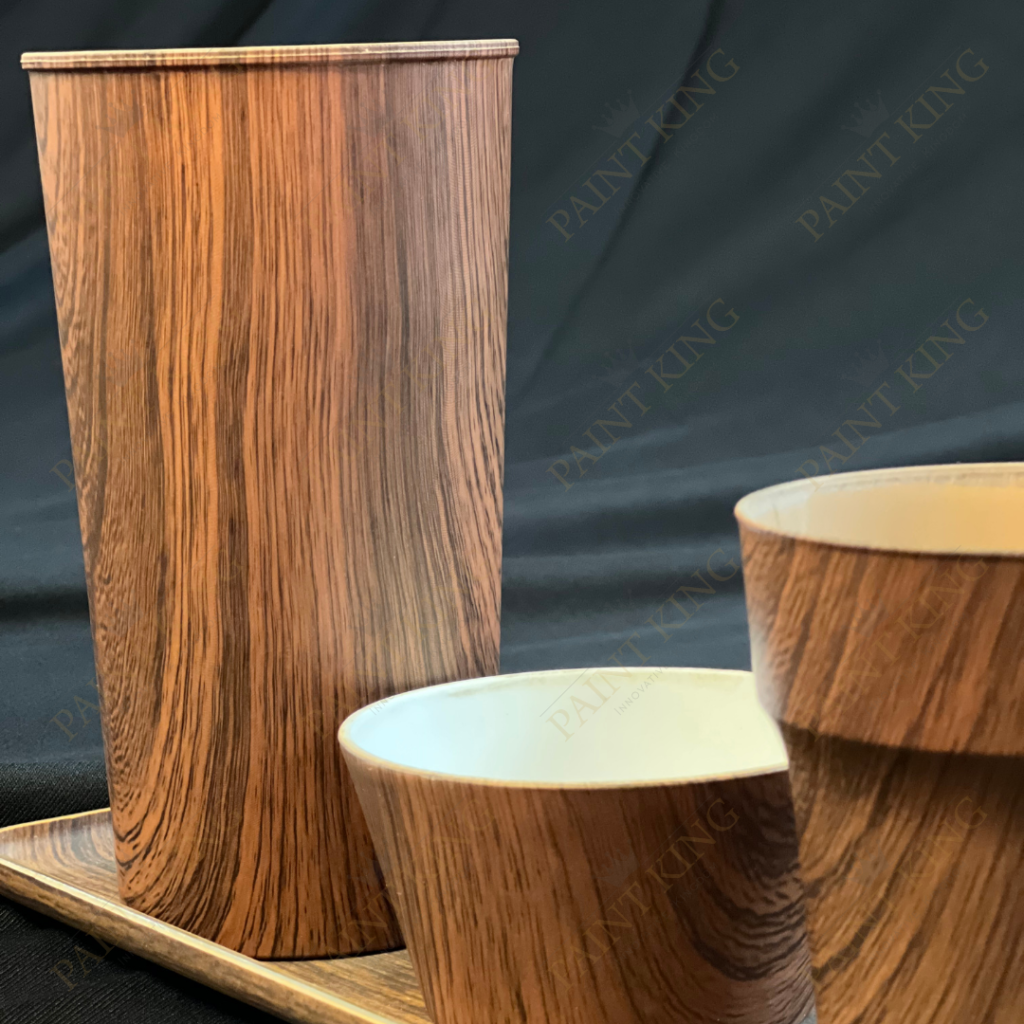
Advantages
Versatility: Hydrographic printing can be applied to various surfaces, allowing customization on plastic, wood, metal, and more.
Customization: Highly customizable designs, including wood grain, carbon fiber, and camouflage, can be applied to 3D objects.
Ease of Application: The process involves priming, applying a base coat, dipping in water, and dissolving the film for pattern transfer.
Durability: Hydrographic prints resist fading and peeling, making them long-lasting and suitable for items exposed to wear and tear.
Aesthetic Appeal: Intricate and realistic designs can be achieved, resulting in visually appealing and unique products.
Cost-Effective: Hydrographic prints don’t fade or peel, reducing the need for frequent replacements, and can be customized in small quantities.
Process
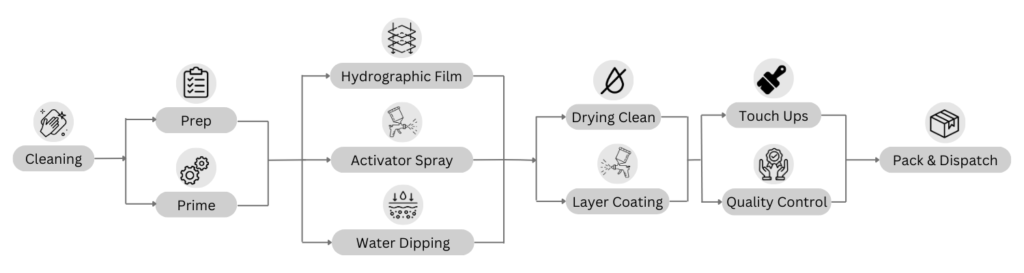
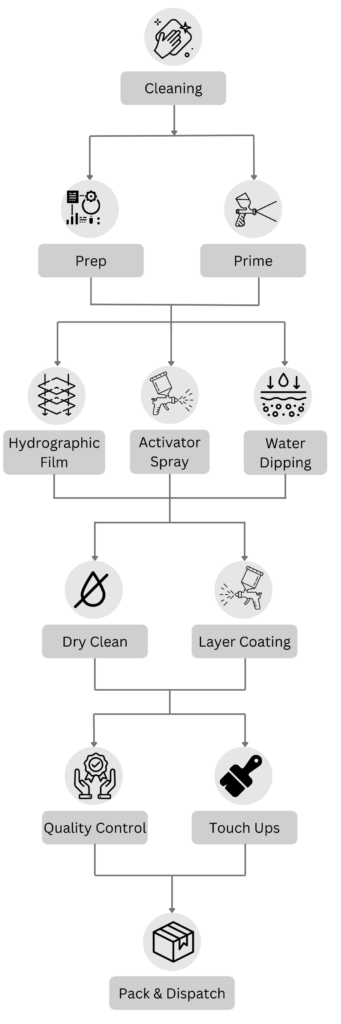
Cleaning: The object is meticulously cleaned to ensure no residues or contaminants are present that could interfere with the printing process.
Prep: Sanding the object creates a smooth surface, which is essential for a uniform application of the primer and the hydrographic film.
Prime: A primer is applied to the prepped surface to enhance the adhesion of the hydrographic film, providing a solid base for the subsequent steps.
Hydrographic Film: A patterned film is laid out on the water’s surface in a dipping tank, ready for the transfer of the design onto the object.
Activator Spray: This chemical agent is sprayed onto the hydrographic film to activate the ink, preparing it for the transfer during the dipping process.
Water Dipping: The object is carefully dipped into the tank, allowing the design from the activated film to wrap around it seamlessly.
Drying Oven: After the dipping, the object is placed in a drying oven where the ink is cured, setting the design firmly onto the object.
Layer Coating: A clear protective coating is applied over the printed design, providing a layer that guards against scratches and environmental elements.
Quality Control: Each object undergoes a thorough inspection to ensure the design has been transferred accurately and that the layer coating is evenly applied.
Touch Ups: If any flaws are detected during the quality control, they are corrected to meet the high standards of the finished product.
Pack & Dispatch: Finally, the object is carefully packaged and dispatched, ensuring it reaches its destination in pristine condition.