Our Services
Explore Endless Paint Services
At PaintKing, we specialize in a diverse range of unique finishing effects for various materials. From the warm allure of Sunwood Finish to the tactile richness of Leather Finish and the innovative Water Dipping (3D) technique, our finishes transform ordinary surfaces into extraordinary statements. Whether it’s plastic or metal, our effects like Texture Silver and Granite Effect provide the perfect touch of elegance and style. We apply our specialized effects on plastics including ABS, PC, PP, HIP, PET, and more, as well as on metals such as steel, aluminum, and brass.
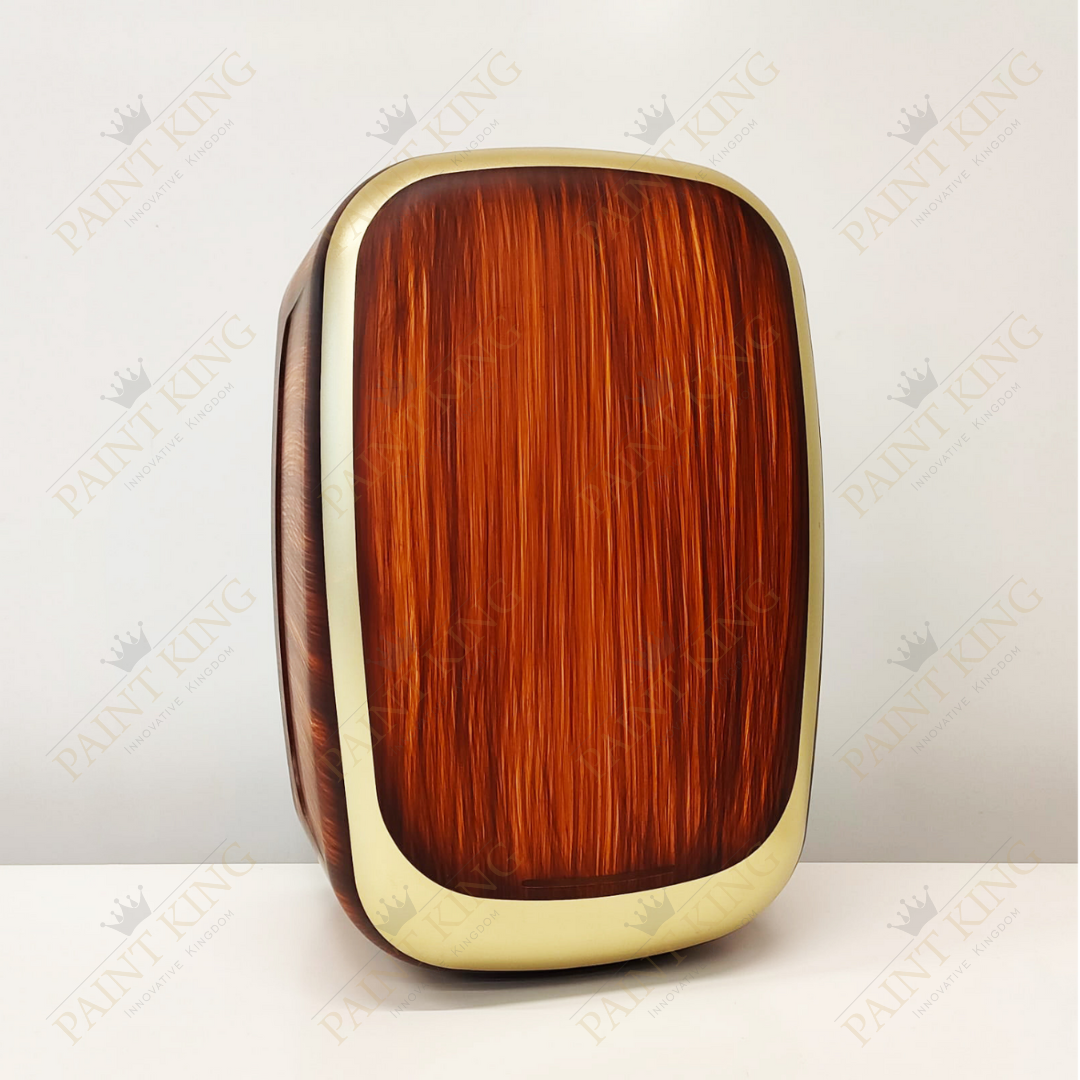
Download Our Product E-Catalogue
Explore our range of coating services across various industries
Explore our extensive range of high-quality paints and finishes. Download our product catalog to find the perfect colors and coatings for your project. From vibrant interiors to durable exteriors, we have everything you need. Let your imagination run wild!
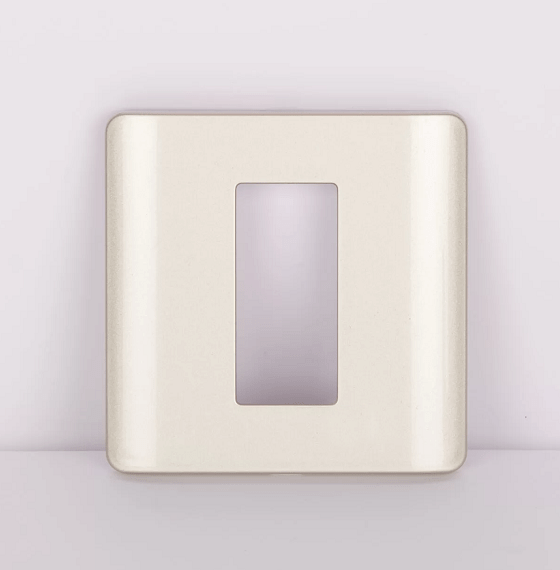
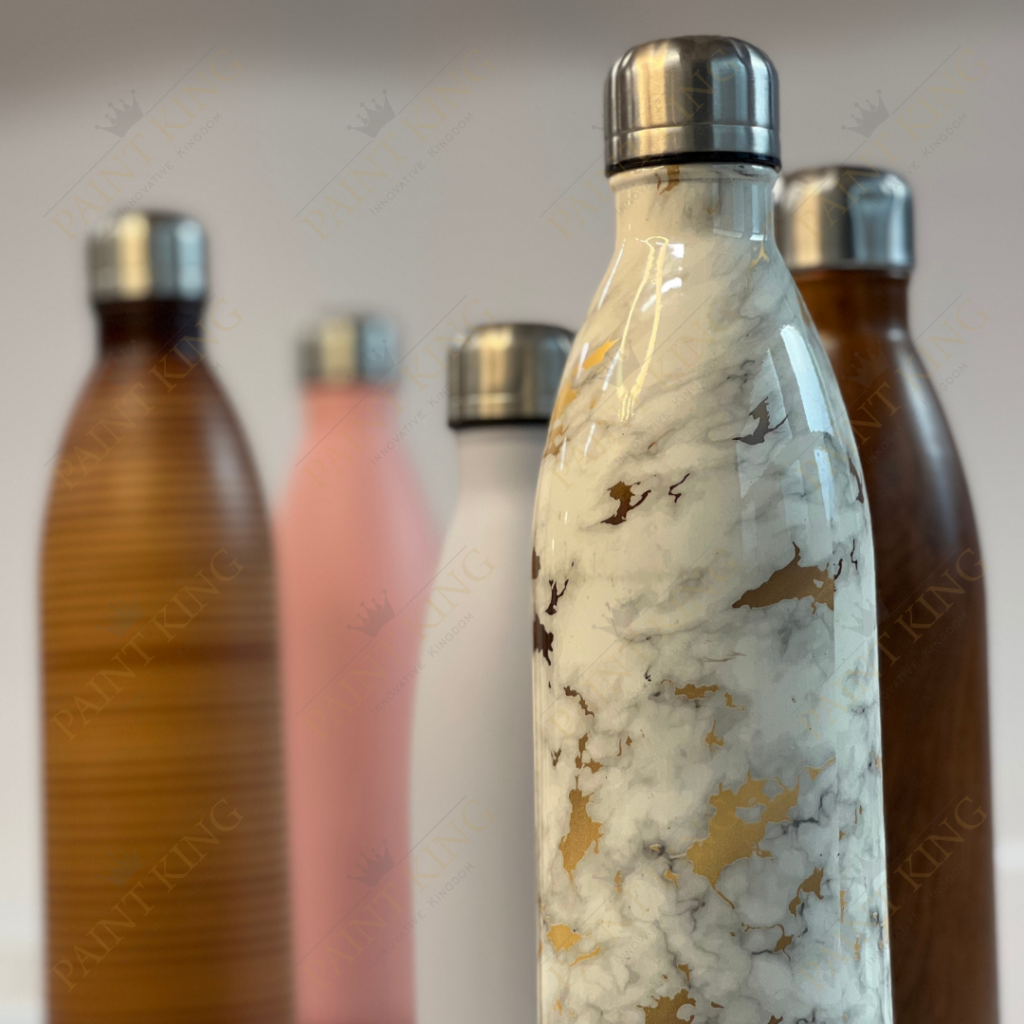
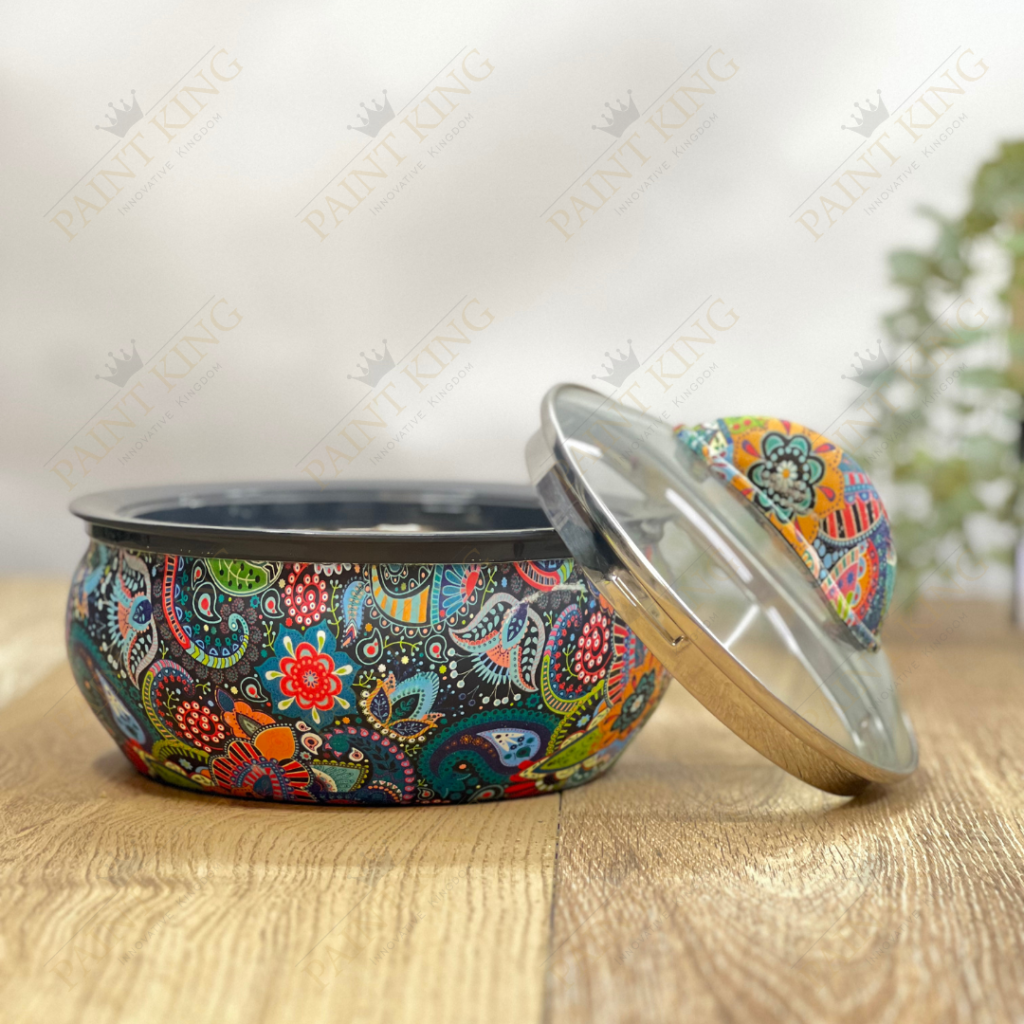
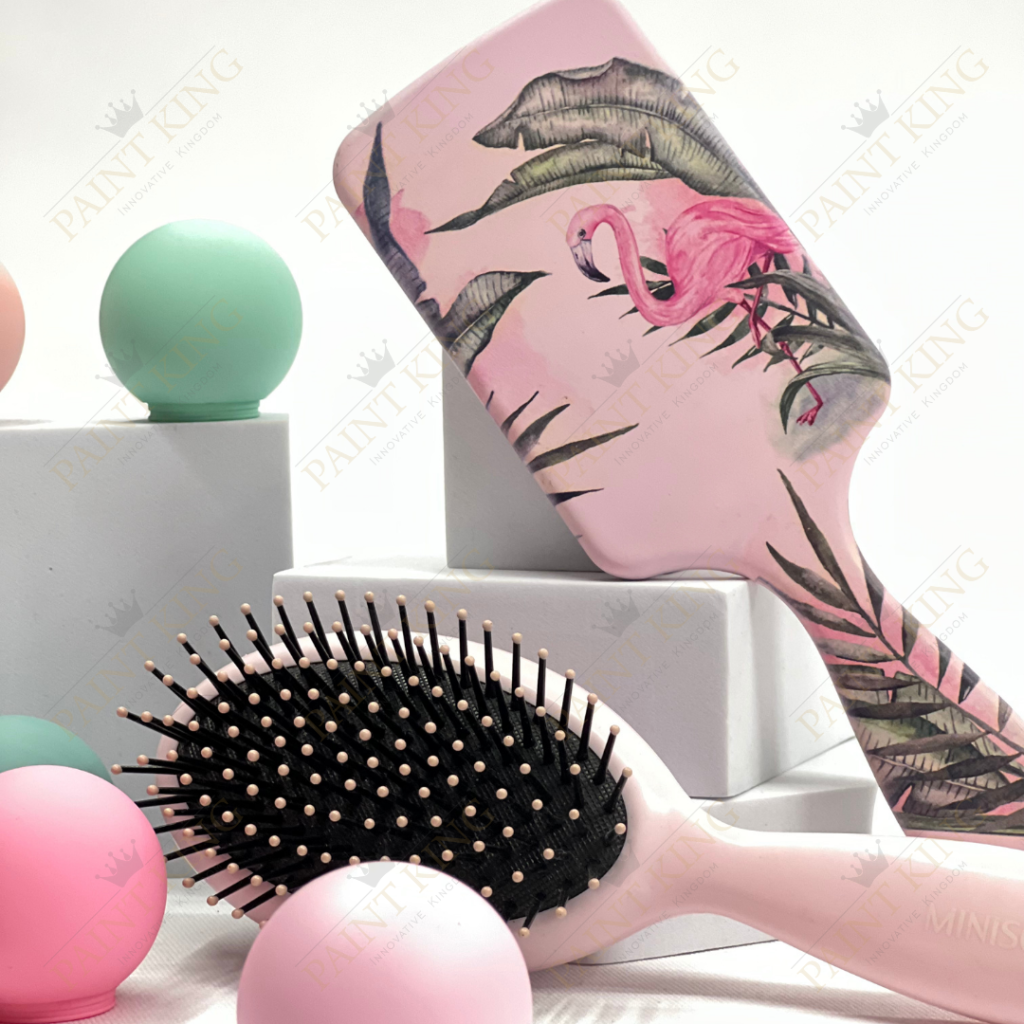
Our Process
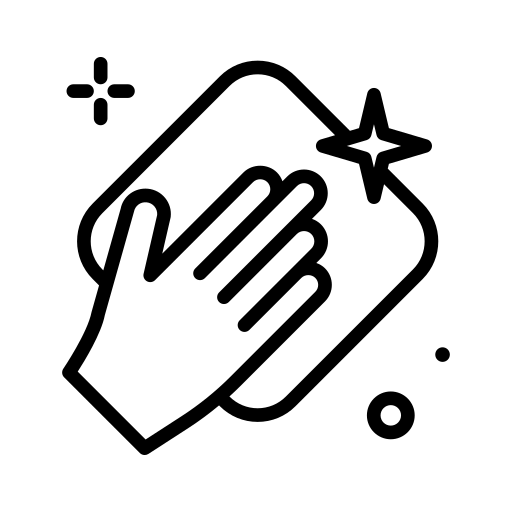
1. Cleaning
Before we start painting, we make sure the surface is really clean. We get rid of any dirt or dust so that the paint goes on smoothly.
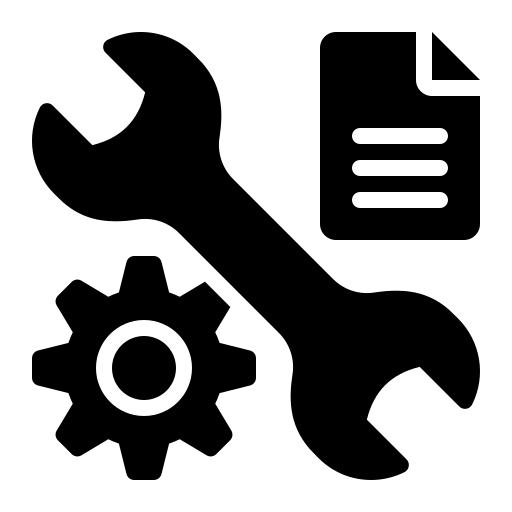
2. Prep & Prime
Once the surface is all clean, we prepare it for painting. We also put on a special paint base, called primer, to make the paint stick better and last longer.
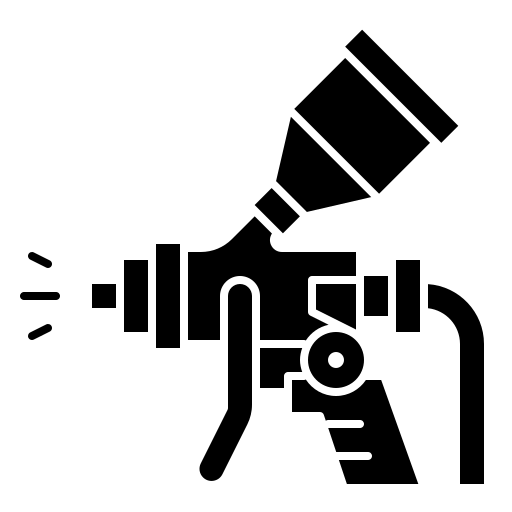
3. Paint
Now comes the fun part! We carefully spray on the paint, making sure it looks really nice and covers everything evenly. We take our time to make sure it looks just right.
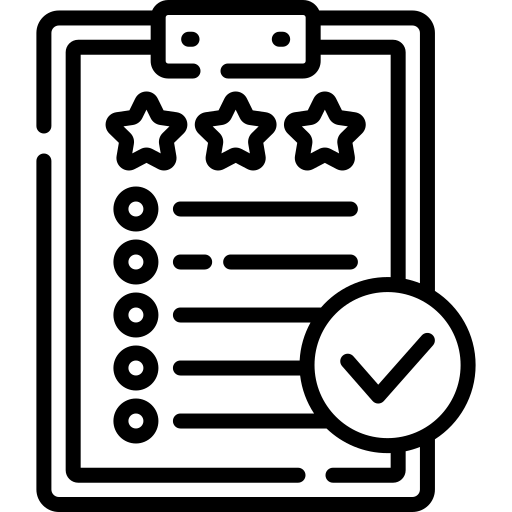
4. Quality Check
After the paint is dry, we take a close look at it to make sure it’s smooth and looks great. We want everything to be perfect before we send it to you.
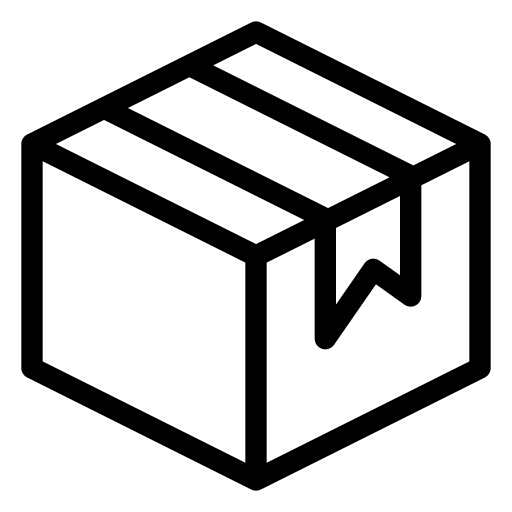
5. Pack & Dispatch
Once we’re happy with the paint job, we pack everything up really nicely and send it to you. We want it to arrive looking just as good as it did when we finished painting it.
Industries we serve
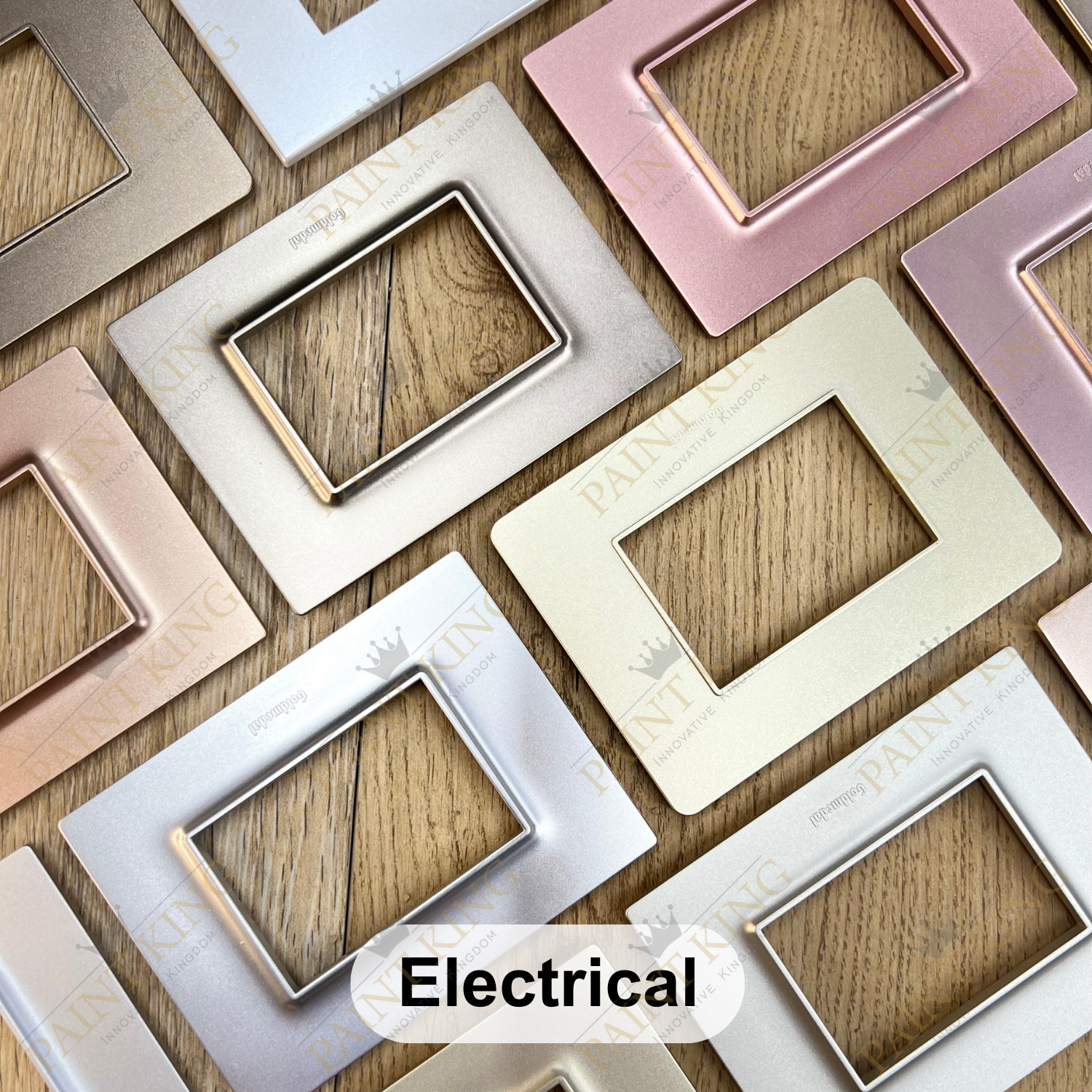
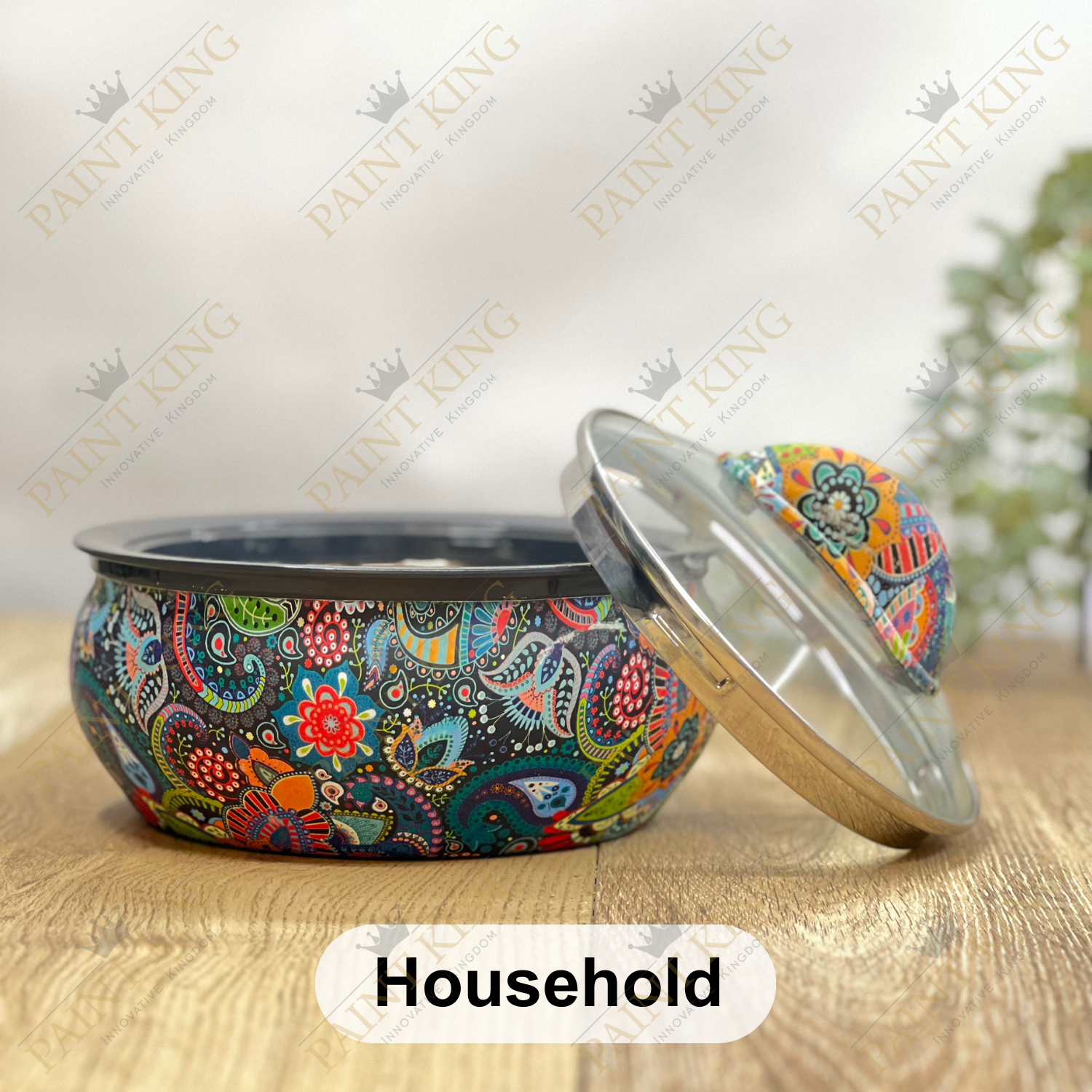
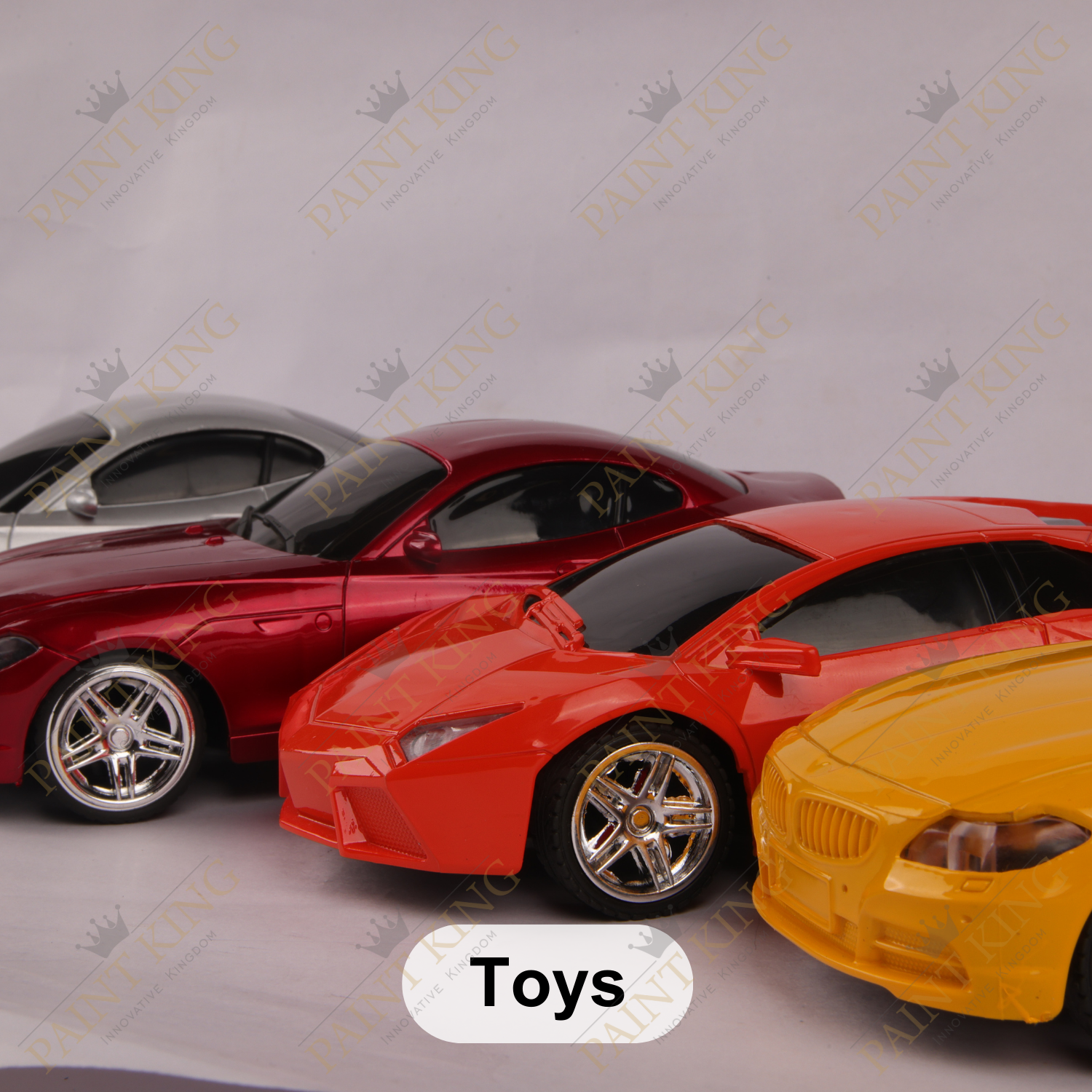
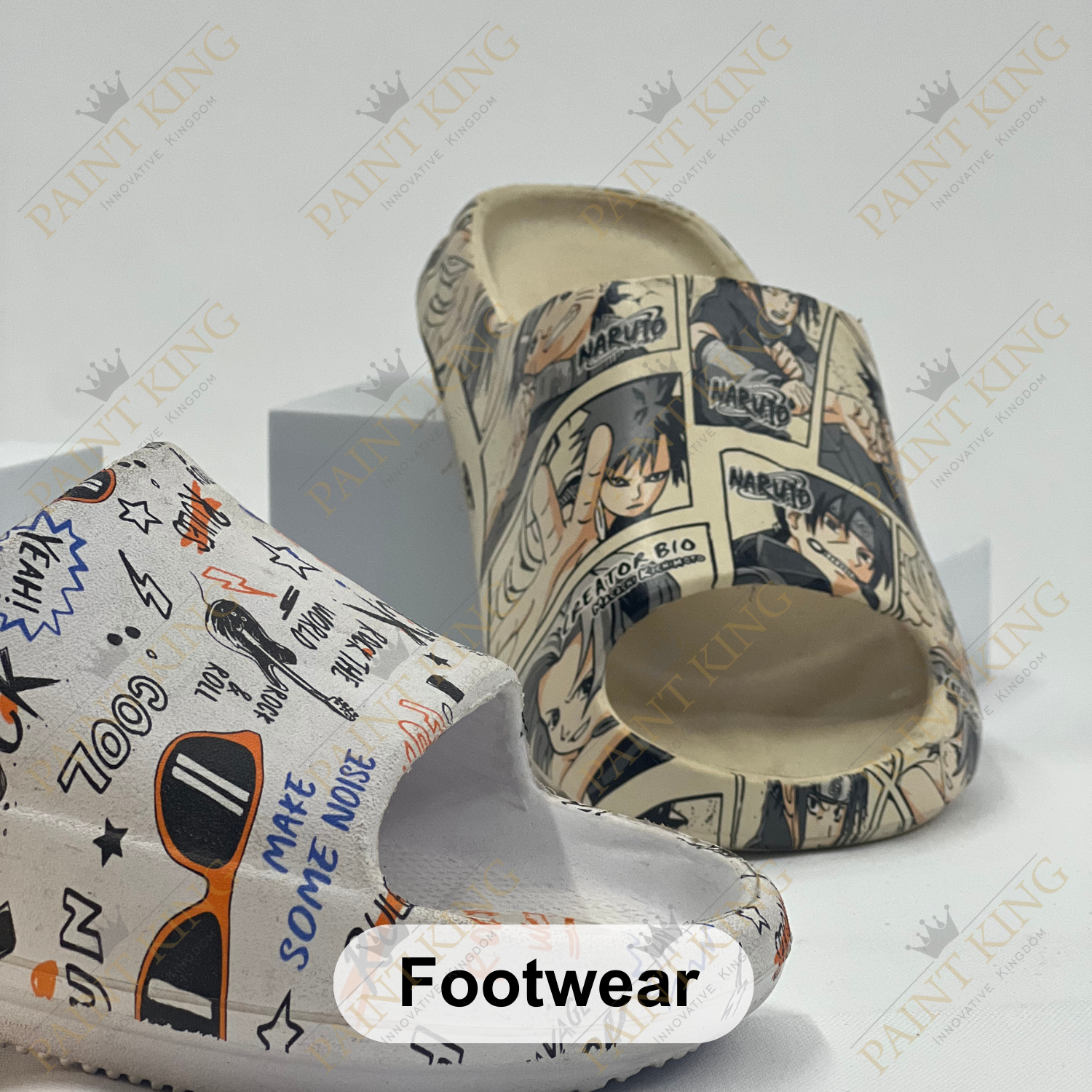
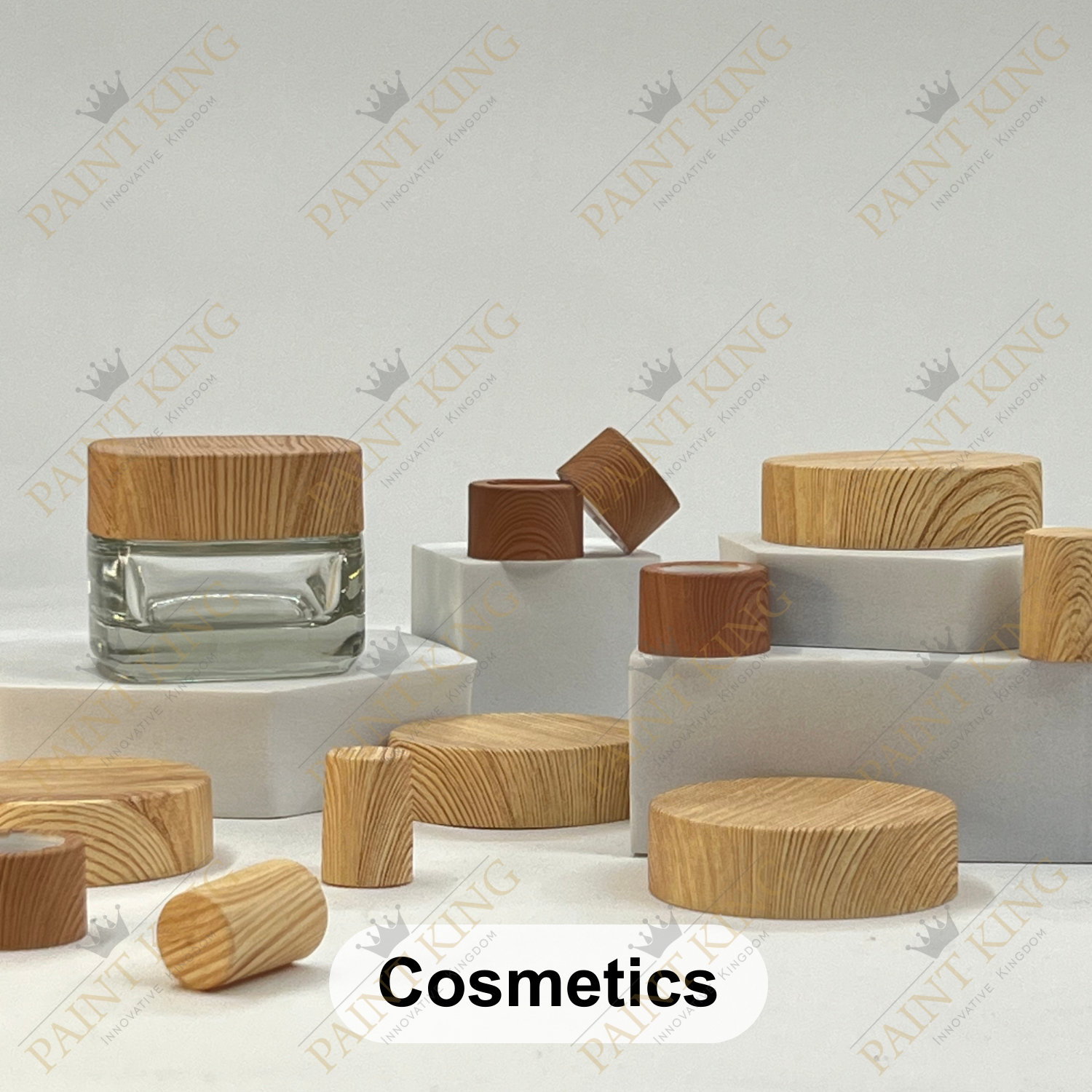
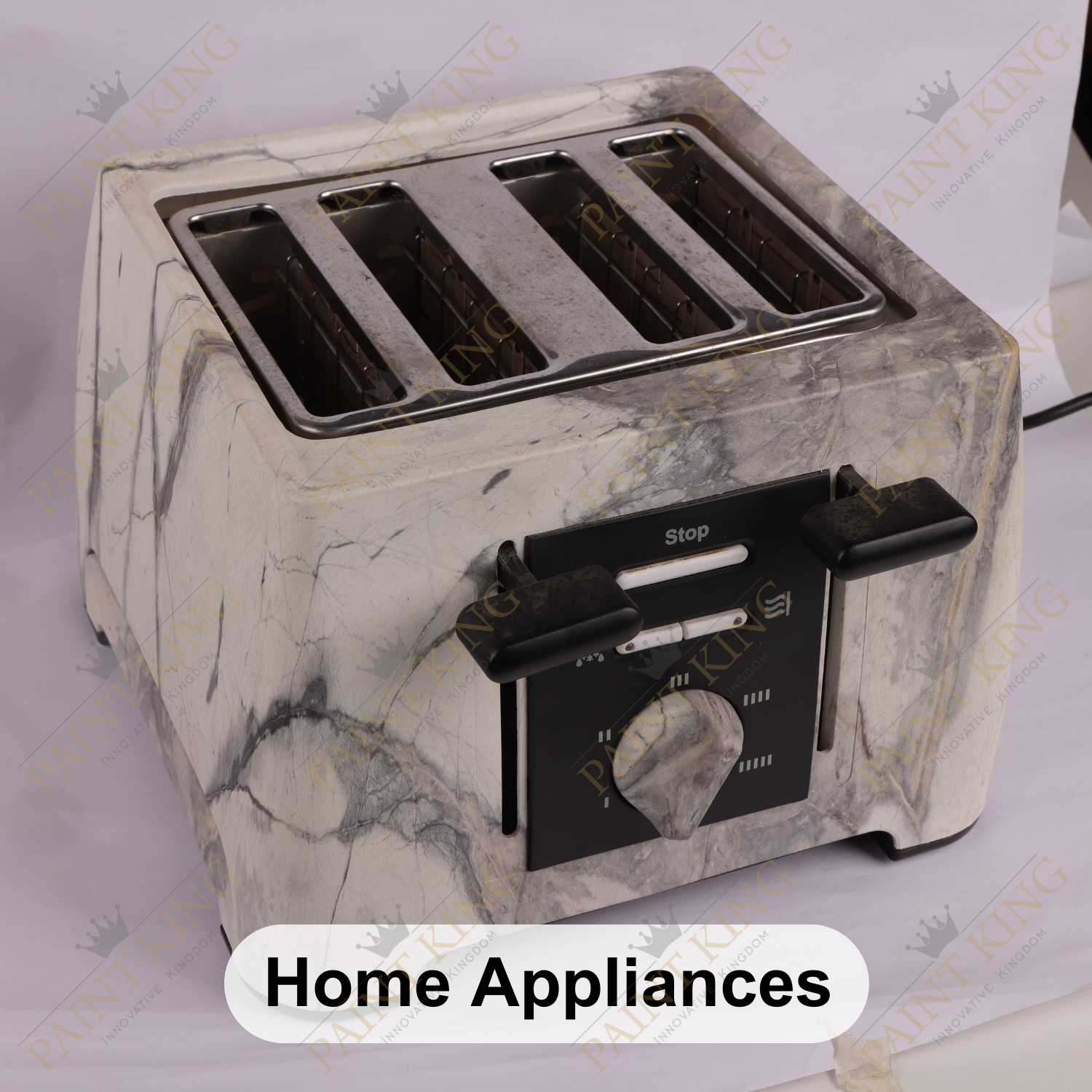
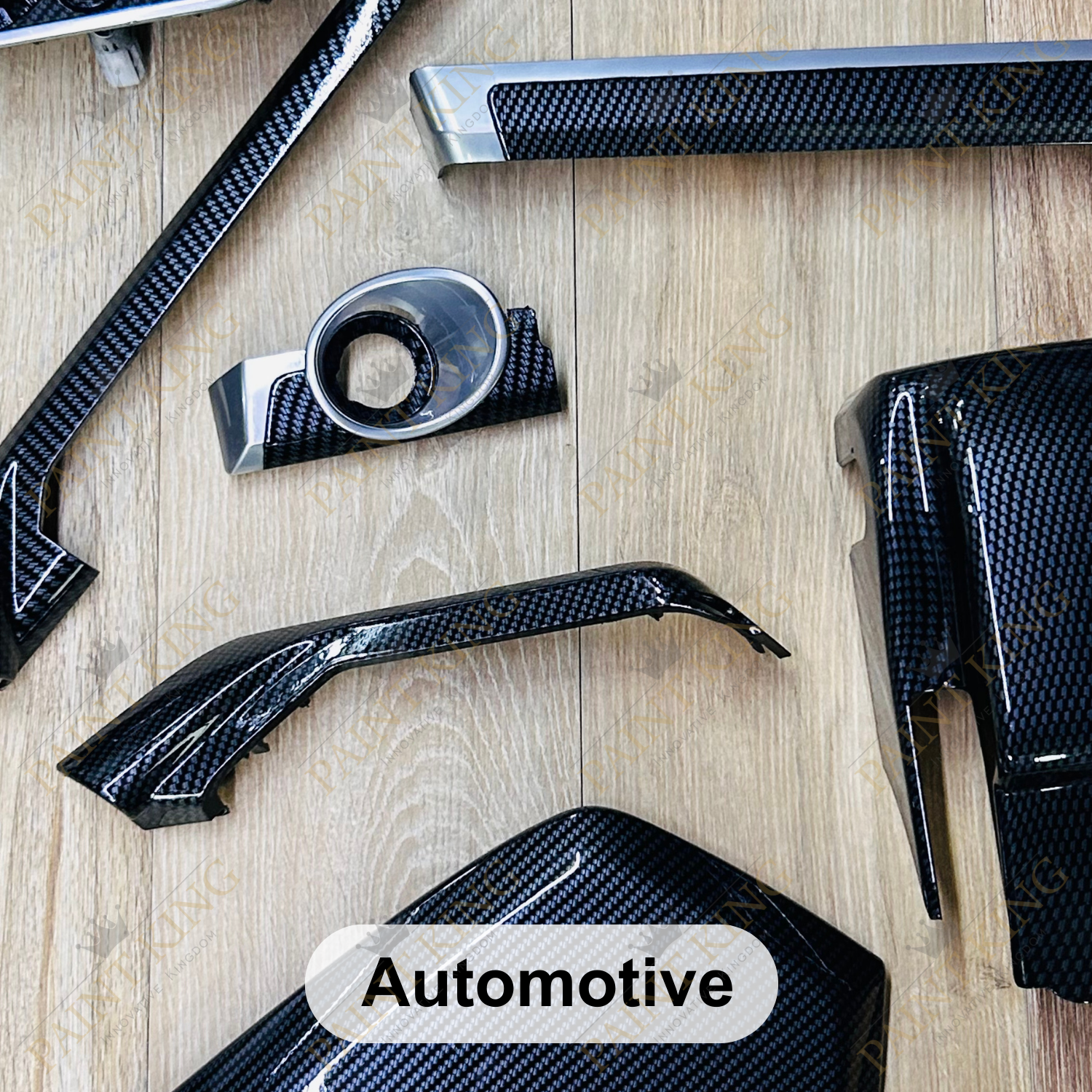
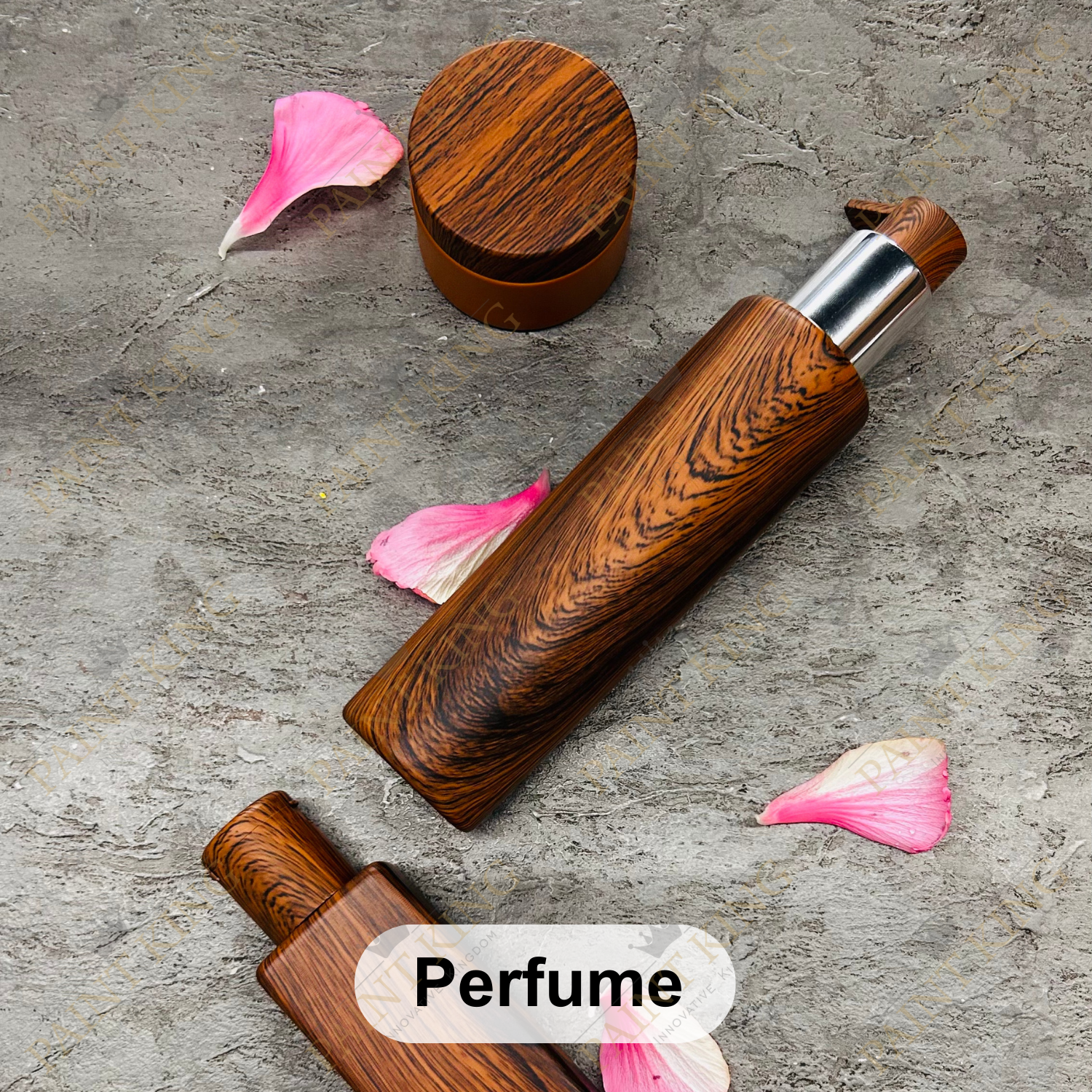
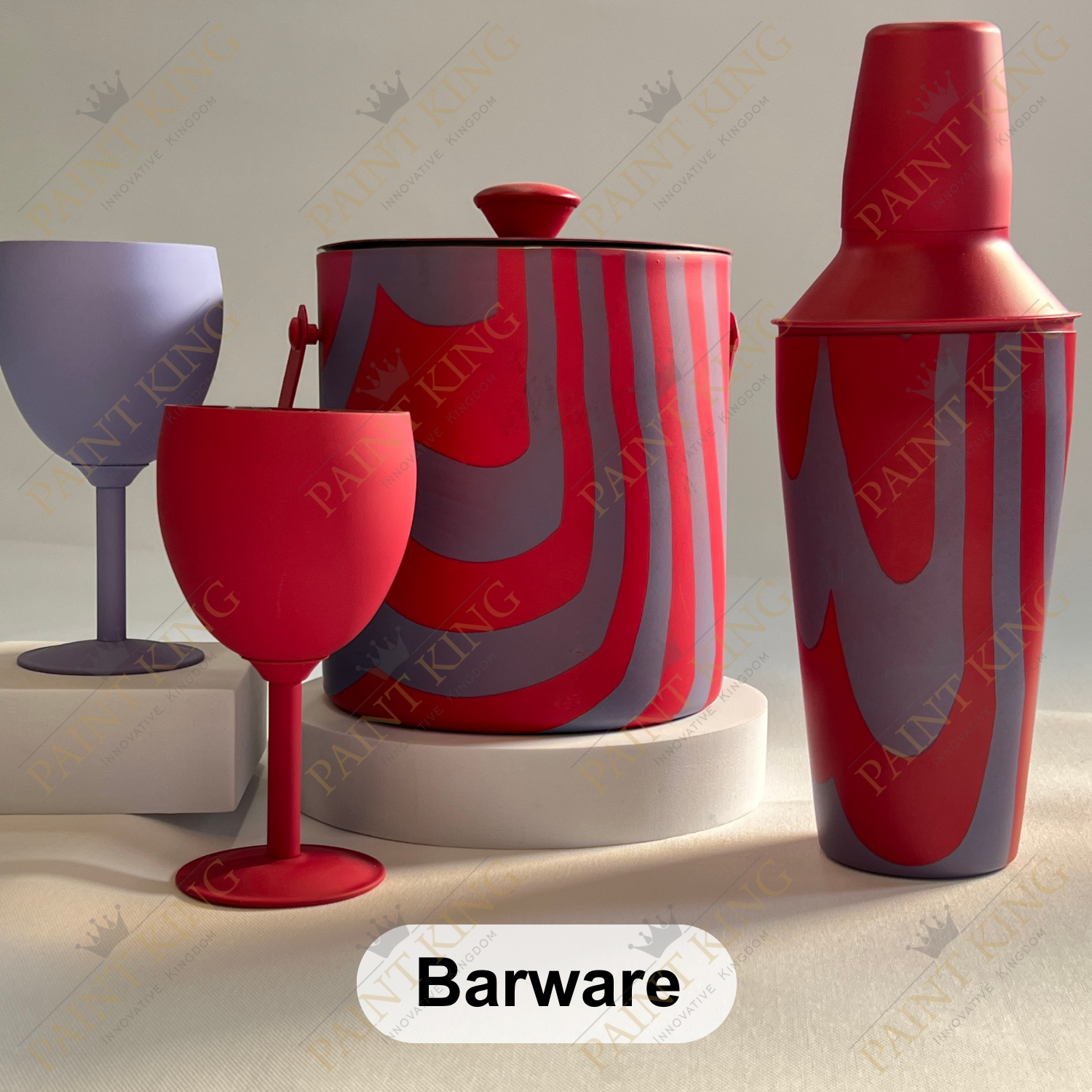
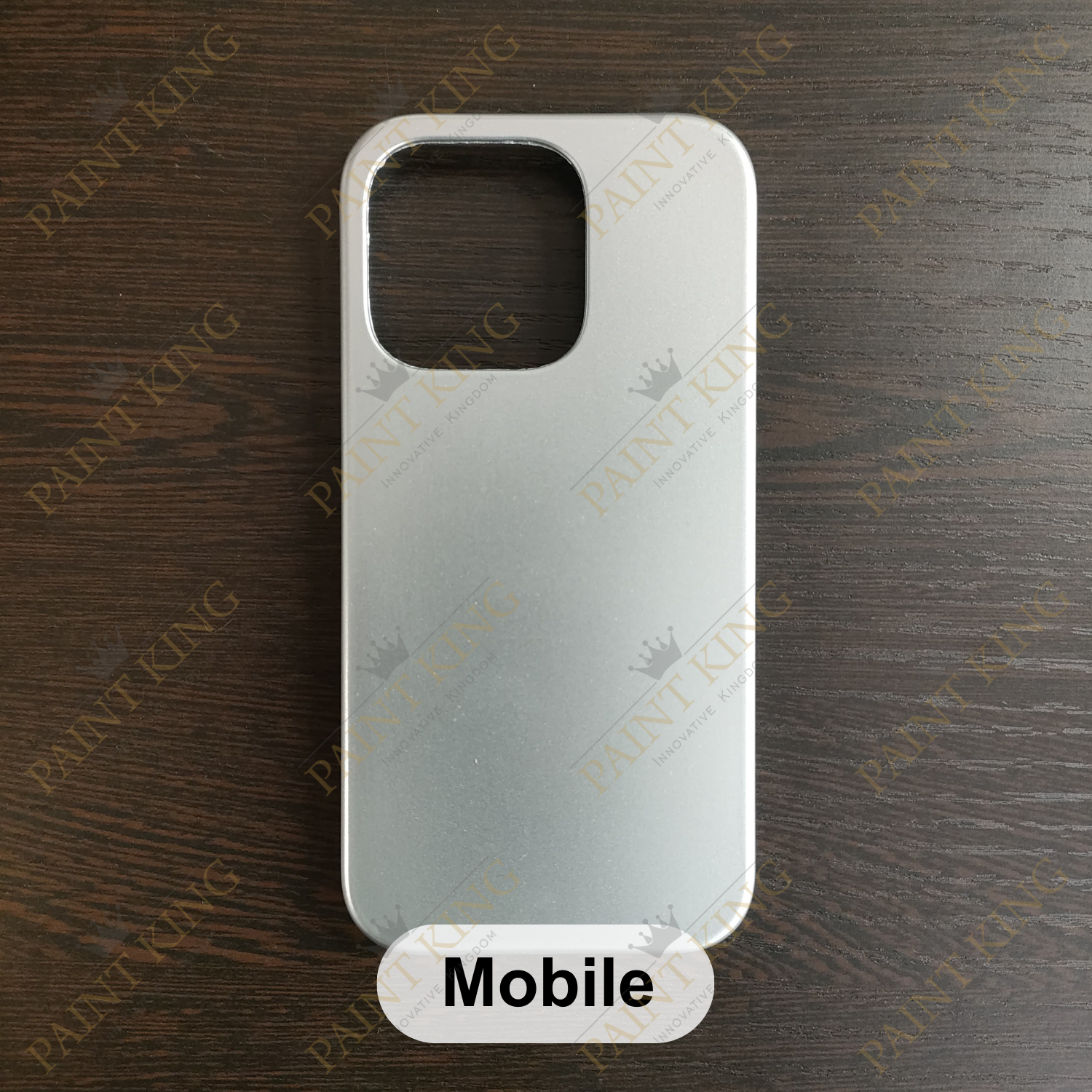
